OUR MISSION
We believe mankind deserves a better parking experience – one with less hassle, with valet like convenience, and one that offers safety and security for themselves and their vehicle.
A complete solution that provides more green space and community places.
A truly workable solution that brings a higher return on capital for investors despite being a responsible and sustainable way to improve the environment.
Therefore, Robotic Parking Systems continues to strive for the highest customer satisfaction by providing reliable technology with true redundancy that performs consistently even under the heaviest traffic demands worldwide.
About Robotic Parking Systems, Inc.OUR PURPOSE
WE CHANGE THE DYNAMICS OF LAND USE.
Parking can make or break a development. Too little, and people stay away. Too much, and you sacrifice valuable commercial space, housing potential, and green areas that enhance the property’s appeal. Robotic Parking Systems solve this problem by storing more cars in less than half the space of traditional garages. This frees land for revenue-generating uses and community amenities—while delivering fast, secure, and user-friendly parking that keeps people coming back.
About Maximizing Land Use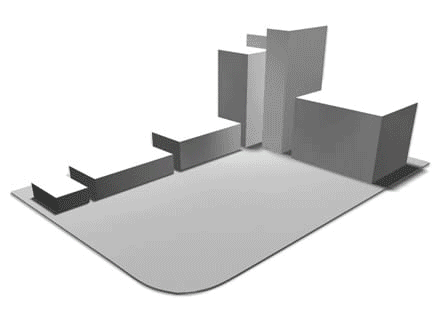
FEATURES:
Fastest vehicle processing speed
Our patented “Lift and Run” technology moves on all three axes simultaneously, making Robotic Systems the industry leader in automotive throughput.
Mobile & Touchless User Interface
Initiate the parking and retrieval process through an NFC, FOB, or mobile app. Users keep their keys in this touchless process, creating a premium valet experience.
Electric Vehicle charging stations
All Robotic Parking Systems can be equipped with EV charging stations as required by the architect and developer. Additional stations can be added at a later date.
Accommodates a wide range of vehicles
Heavyweight or low profile, Robotic Parking Systems’ patented pallet technology allows us to accomodate and effectively move vehicles the competition does not.
First and Last Impressions Count
With a Robotic Parking System the arrival and departure plaza can be easily blended into the overall architectural theme of the development.
Founded in 1994, US-based Robotic Parking Systems, Inc. pioneered the development of the high-capacity, scalable automated parking garage, opening a new vista in the parking industry.
A robotic parking system reduces the space needed for cars by 50% or more, creating more space for design and development, and in the environment, room for more green spaces. While automated parking has been in development since the early 20th century, the patented and scalable robotics that Robotic Parking Systems’ brought to the industry allowed the benefits of automated parking to be applied to projects requiring hundreds and even thousands of parking spaces.
The management team of Robotic Parking Systems incorporates more than 70 years of cumulative competence in the development, the construction and the operation of automated transport systems. Strategic partnerships with notable high-tech automation firms ensure that Robotic Parking Systems remains at the forefront of one of the most exciting fields in the 21st century construction industry by continuing to develop state-of-the-art electronic management and control systems.
All Robotic Parking Systems’ machinery is manufactured at the company’s headquarters in Clearwater, Florida, USA. The company has the only full-scale manufacturing facility in North America dedicated to designing and building custom automated parking garages. We are not an OEM or distributor. We manufacture our machinery from raw steel to finished product using off-the-shelf components primarily from US distributors.
Quality control is maintained using our 114-car research and testing garage located within our 100,000 sq. ft. production plant. This facility allows us to test and certify every machine before it’s shipped to the customer’s job site.
Patents
Robotic Parking Systems’ high-speed, efficient automated parking technology is patented in the United States and in countries around the world. Additional patents are pending. Recent patents include high speed fire containment technology that makes our parking garages the safest in the world, and pallet cleaning technology that cleans up snow, ice and debris from pallets between uses–critical for winter environments.
US Patents
![]() |
Patent Number US 12,180,740 B2 Patent Number US 6,851,921 B2 Patent Number US 6,662,077 B2 Patent Number US 6,502,011 B2 Patent Number 5,669,753
|
“The Hoboken municipal parking garage that opened its robotically controlled doors last year displays a stunning agility. It lifts and carries cars about on computer-controlled steel pallets as if they were delicate ballerinas, moving with precision and speed inside a structure that is remarkable compact…'[A]mazingly proficient use of space… “It may provide one of the solutions to the most important conflict in urban design: where do you put all the cars in environments where car volume is high and space is at a premium?”
“When you return— no guesswork about where you parked it, no strange nicks, dents, or scratches… and no parking attendant to tip.”
“”I would rather go without food than without this garage.”
“One of the top ten parking garages in the world.”
“One of the best inventions of the 20th century.”
“I am extremely pleased with the quality and professionalism of Robotic Parking System’s work, as well as the attention to detail.”
“Great company in every aspect — professional, with great attention to safety and quality. We highly recommend them for any automatic car park.”
“Robotic Parking is changing the dynamics of land use.”